6000 parts, 230 strings, 18 tonnes of tension – are your pianos up to the task of music education?
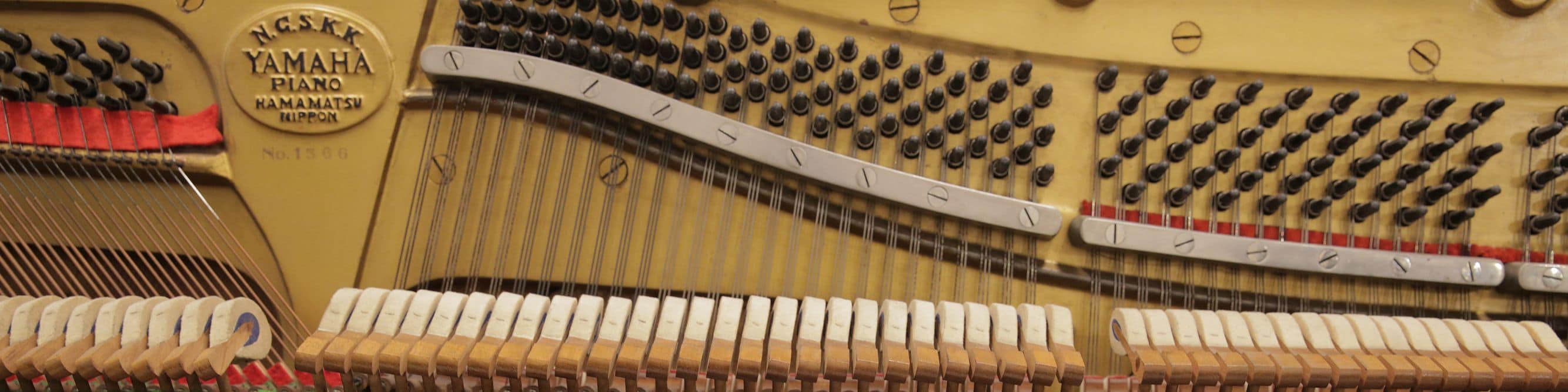
Julian Morgan-Smith - Piano Technical Manager – Yamaha Music Australia
Piano Technical Manager – Yamaha Music Australia
As an education and facilitator of piano education, I believe it is important to understand how the technical aspects of acoustic pianos can affect the playability, usability and lifespan of the instrument.
The number one enemy of pianos is common to all of us: age. Due to the sheer complexity and number of moving parts in pianos, they unfortunately do not improve over time. Much like cars, the friction points wear out, the materials degrade and, without proper servicing, the piano will quickly fail to function properly.
6000 parts

The sheer complexity of a piano’s mechanism is often overlooked by nature of it being hidden from view. It’s surprising the number of times I’ve removed the front board of an upright, or the keyboard out of the grand piano and the piano teacher states: “I’ve never seen that before!”
I actively encourage music educators to learn how the inside of a piano works. There’s no expectation to become an expert – that’s what piano technicians are for – but a basic understanding of how to assess a piano’s quality and condition is an important skill to have.
How do we know if a piano is suitable for education? The most comprehensive way is to engage the services of a piano technician to carry out a condition report. Before we do that, however, here are some basic points to check over when assessing a piano:
Age: How old is the piano? Printed on the iron frame of most pianos will be a serial number unique to that piano. A quick search online for a piano age calculator should help you here.
Keyboard: What condition are the white and black keytops in? Chips, uneven heights and rough surfaces negatively affect the playability and feel of a piano.
A less obvious aspect to watch out for is the state of the key bushings. Key bushings (Figure 1) are made from cloth which sit within the mortises of the wooden keys, between the wood and the pins on the key frame. Pick a few sample keys, hold one down halfway through the keystroke and wiggle it from side to side. If there is more than 1mm of movement in either direction, the key has worn front bushings. The job of these bushings is to smoothly guide the key in the vertical plane. As they wear, the keys are able to move in a horizontal plane, giving the keyboard a “loose” feeling. This affects fine control of piano playing quite substantially – if you’ve spent a lot of time playing on a worn-out keyboard, you’ll definitely notice the difference when you play on one in good condition!
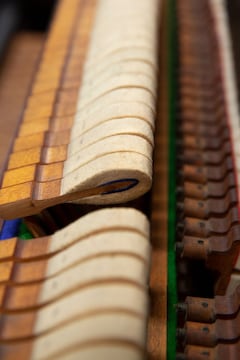
Hammers: The piano consists of three primary means of tonal production – the hammers, strings and soundboard. At the start of the playing process the hammers strike the strings which, in turn, vibrate the soundboard. Due to the hammers being in a fixed position when the instrument is played, the strings over time will start digging grooves into the hammer felt, flattening the striking surface and hardening the felt. Part of a piano technician’s job is to “voice” the hammers through different means of needling, sanding and filing, in order to maintain a piano’s quality of tone. It can be difficult to assess a piano’s tone without experience, but a few basic things to check for include the following:
Consider the overall tone or colour. Is the piano bright or mellow? Is that tone consistent across the keyboard range? Does the tone change between playing pianissimo and forte, or does only the volume change? You can also open the top lid on uprights (or look between the strings on grand pianos) to visually inspect the hammers. Are there deep grooves on the striking surface? Is the striking surface round or flat? Are the hammers striking the strings in the centre, or are the string grooves off to one side?
I strongly believe that voicing the hammer is just as important as tuning the strings. Without a controllable and consistent tone, you dramatically decrease the pianist’s ability to express their interpretation of a piece of music.
Action regulation: Pushing down a piano key and hearing the hammer strike is a simple enough process, but inside the piano hundreds of moving parts are working together to deliver this movement. Piano manufacturers construct the keyboard mechanisms in a way that allows piano technicians to adjust how these parts interact with each other. This adjustment process is called “regulation”, which, when done well, results in a piano keyboard that “feels invisible”. The pianist should not need to constantly adjust their technique to suit the piano – the piano mechanism should simply become an extension of the musician.
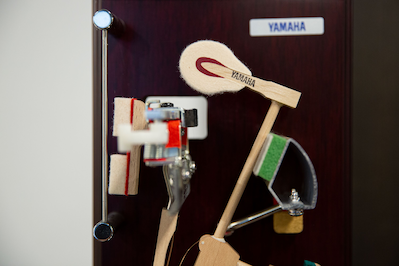
As piano mechanisms are mostly constructed with wood, felt, cloth, leather and other organic materials, the previously mentioned aspects of age and wear start to take their toll. Without launching into a lecture on piano regulation (grand pianos have ~35 procedures, per key), there are some basic things to look out for.
Try and analyse how the keyboard feels. How softly can you make the hammer strike the string? Is this consistent across the keyboard? By lifting the top lid of an upright or looking between the strings on a grand, slowly depress a key and watch the hammer move. As it nears the string at a certain point, the hammer will disengage and fall back. The distance between hammer and strings at which the hammer disengages is called “let-off” and should be 1–3mm. If this distance is significantly greater and/or is inconsistent across all the hammers, the keyboard will feel unpredictable and difficult to control in the pianissimo register.
Other regulation procedures – such as key height, key depth and “hammer to string” distance are equally as important, but are difficult to assess without training, so these would be best checked over by a piano technician.
230 strings
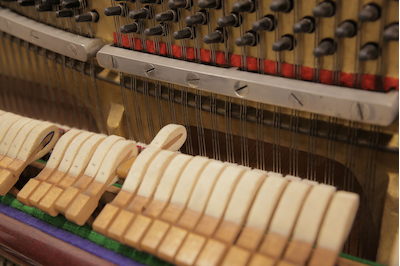
230 strings
We all know that pianos should be tuned at least once per year, and more often if they are used in a professional or institutional setting. The development of pitch is crucial in the beginning stages of a musician’s education. Although piano players aren’t in control of their instrument’s intonation, an internalised sense of the correct pitch will inform aural skills in later stages of a student’s musical career.
When checking a piano’s viability for education, it is worth considering the condition of the ~230 strings. Severely corroded or pitted strings will have an increased chance of breaking during normal use and tuning. A corroded string is also more difficult to tune to a “stable” condition, as the various contact points either side of the speaking length can “bind”, causing unequal tension across the entire length of the string. Strings in upright pianos tend to fare better over time due to them being boxed in by the cabinet. Grand pianos, by virtue of being opened up more frequently when played, can experience string corrosion from the environment – a good reason to fully close up the instrument when not in use!
18 tonnes of tension
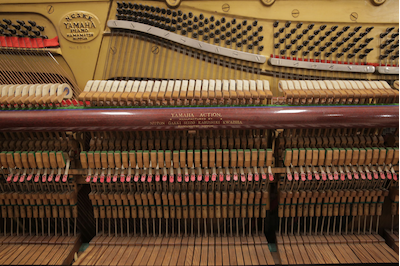
18 tonnes of tension
The constant stresses imparted by the collective tension on all ~230 strings to the frame, soundboard and bridge are not insignificant. Combined with the complex mechanism, we can start to see how a piano does not age well over the years. Most schools and institutions will engage with a regular piano technician to perform an annual tuning of the piano fleet, but is this enough?
In reality, a piano that is simply being tuned is not being improved. In fact, you could argue that it’s not even being maintained. Without additional maintenance, it will experience tonal and mechanical degradation as the years pass by.
True maintenance of pianos requires more than just tuning; voicing, regulation, cleaning and refurbishment of the high-wear items are crucial in order to prolong an instrument’s quality of sound and touch. It is highly recommended that a school or institution should build a relationship with a quality piano technician and, in the beginning stages of that relationship, carry out a condition report on the fleet of pianos. This will allow the technician to formulate a 5-year, 10-year or even 20-year plan for the instruments, which could include a basic tuning and servicing schedule, refurbishment intervals and long-term replacement plans. This will ultimately make budgeting and planning easier in the long term, while providing a higher quality music education experience for both teachers and students.
Julian Morgan-Smith - Piano Technical Manager - Yamaha Music Australia
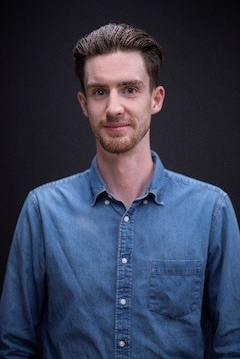
Julian Morgan-Smith - Piano Technical Manager - Yamaha Music Australia
Julian Morgan-Smith is the Piano Technical Manager at Yamaha Music Australia. Julian has been a piano technician for 10 years, receiving his initial training at the Australasian School of Piano Technology in Melbourne, before he went on to work as a self-employed technician. Julian has since worked in Sydney as a technician at the Steinway & Sons dealership, Theme and Variations Piano Services. Julian returned to Melbourne before working at Yamaha Music Australia in 2019, where he furthered his training at the Yamaha Piano Technical Academy in Japan, achieving Grand Master technician status.